Constant axle issues! We feared a faulty trailer frame was to blame.
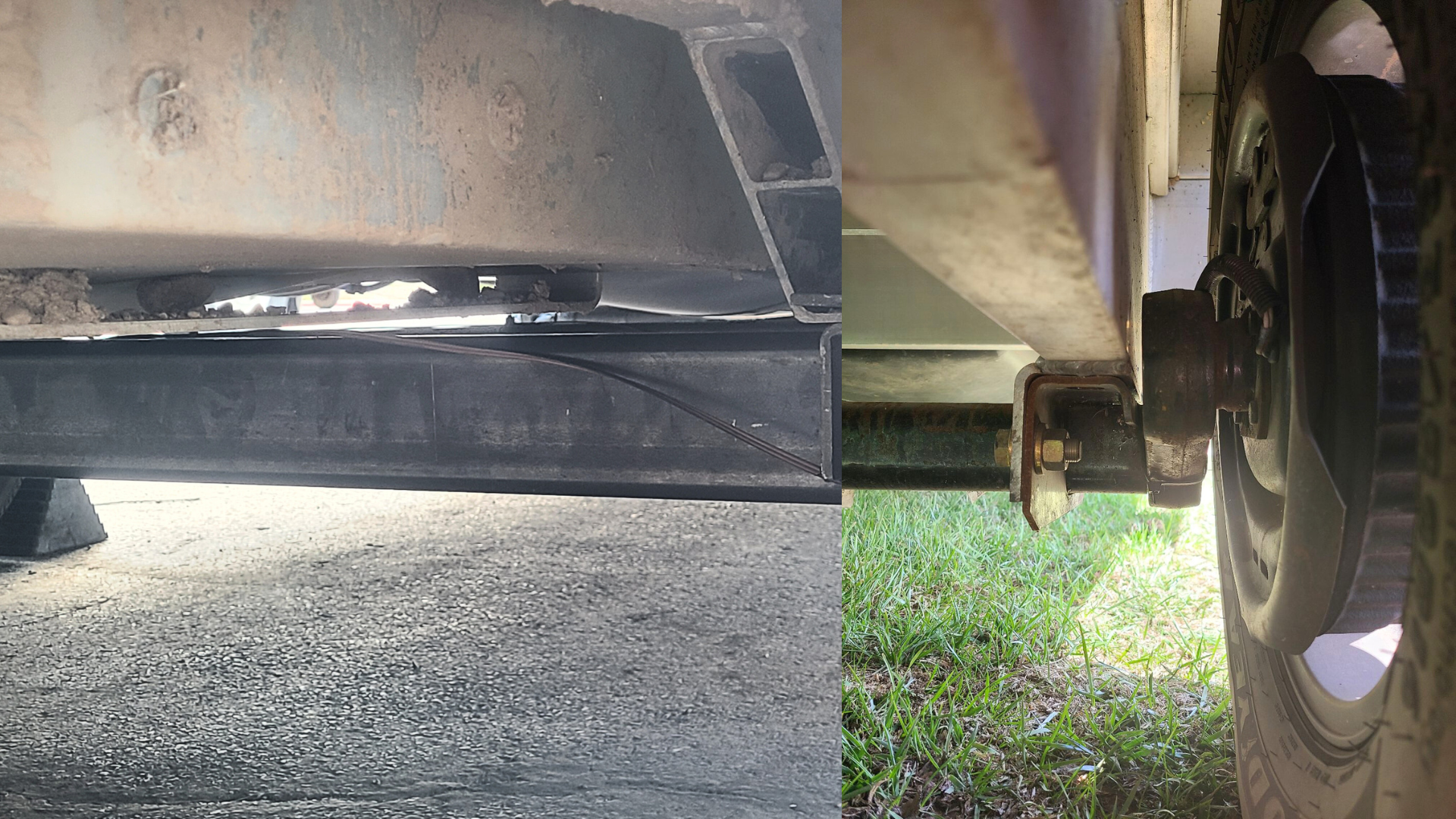
We often have fellow RVers ask us when we purchased our RV. We tell people that we custom ordered it in 2020 and took delivery in 2021. Questions immediately follow: "Oh wow, how has it been so far?" "Ooph, have you needed lots of repairs?" They ask this because we bought the rig new, and yes, it was a "COVID build." This is RVer-speak for an RV that was built during the time when manufacturers and parts suppliers were overwhelmed by the uptick in sales. The other side to it, buying the rig new, has other underlying theories from well before the pandemic. If you buy new, you will need a "shakedown period" where lots of things will break and need fixing. Furthermore, RVs "aren't built how they used to," meaning that more corners are being cut and details are being overlooked.
Fortunately, we don't follow any of these expected norms. Our manufacturer, ATC, only began building recreational trailers relatively recently, after years of focusing on industrial builds. The overwhelm was certainly real, but this resulted in a setback of our time until completion. Once we got the trailer, mostly everything functioned just fine and the build was high quality. We also didn't have a shakedown period, at least not right away. We joked last year that our shakedown period came late, right when most warranties were expiring. These were mostly third party items breaking, like our toilet and our microwave.
The trailer itself, though, held strong. No matter what repairs needed to get done, we trusted the quality of our build, and we have felt totally safe towing our ATC toyhauler tens of thousands of miles over the past few years.
That was until we found ourselves in a disconcerting series of events. Last year, we stopped at our solar contractor's property in Arizona to get our install, when he noticed a bit of uneven wear on one of our trailer tires. It was on the inside and not easy to spot, and it looked like gradual wear over time, so we missed it during our tire checks. With Boondoctor John's fresh eyes and more astute attention to detail, he noticed the wear right away. He guessed that it might be an axle problem and advised us to get someone to look at it. We spent a couple of months tracking down the right person to give us an assessment, finally finding someone outside of Provo, Utah.
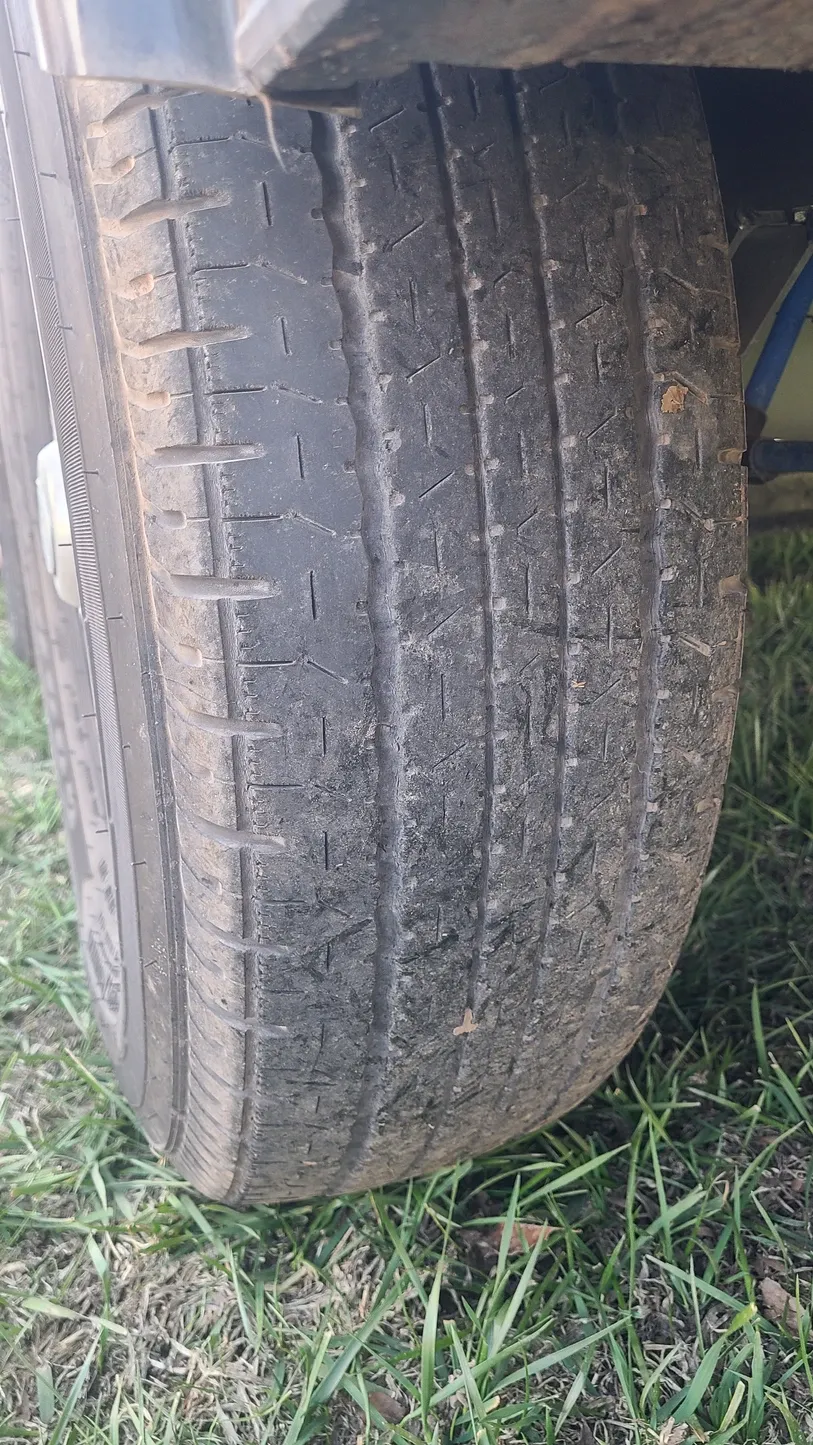
We planned our travels around the axle assessment, setting up camp at Spanish Fork River Park, where Garret our axle dude would come to us. We didn't know what to expect. If it was an axle problem, how did it happen? Boondoctor John suggested that it was due to weight distribution problems, specifically being too heavy in the front, which is common with front bedroom trailers. We got a four-corner weigh the following month. As John expected, our front was heavier, but not to an alarming extent. We were also a little heavier on the driver's side, which we were told is seen in the vast majority of RVs because the kitchen and bathroom are both usually on that side. Otherwise, we were so balanced that the people who weighed us thought we had done a four-corner weigh before and were impressed that it was our first time. We were proud.
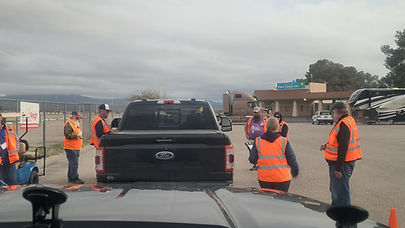
So while some uneven distribution could have been the culprit, we didn't think that was the whole story. We also considered that our hitch might not be distributing weight properly because it had been installed incorrectly the day we picked up the RV. Could all of this add up to cause irreparable damage to the axles?
Unfortunately, Garret gave us the worst news: We would need both axles replaced. One was bent and the other had a broken part. We made an appointment with a nearby FleetPride to get new axles.
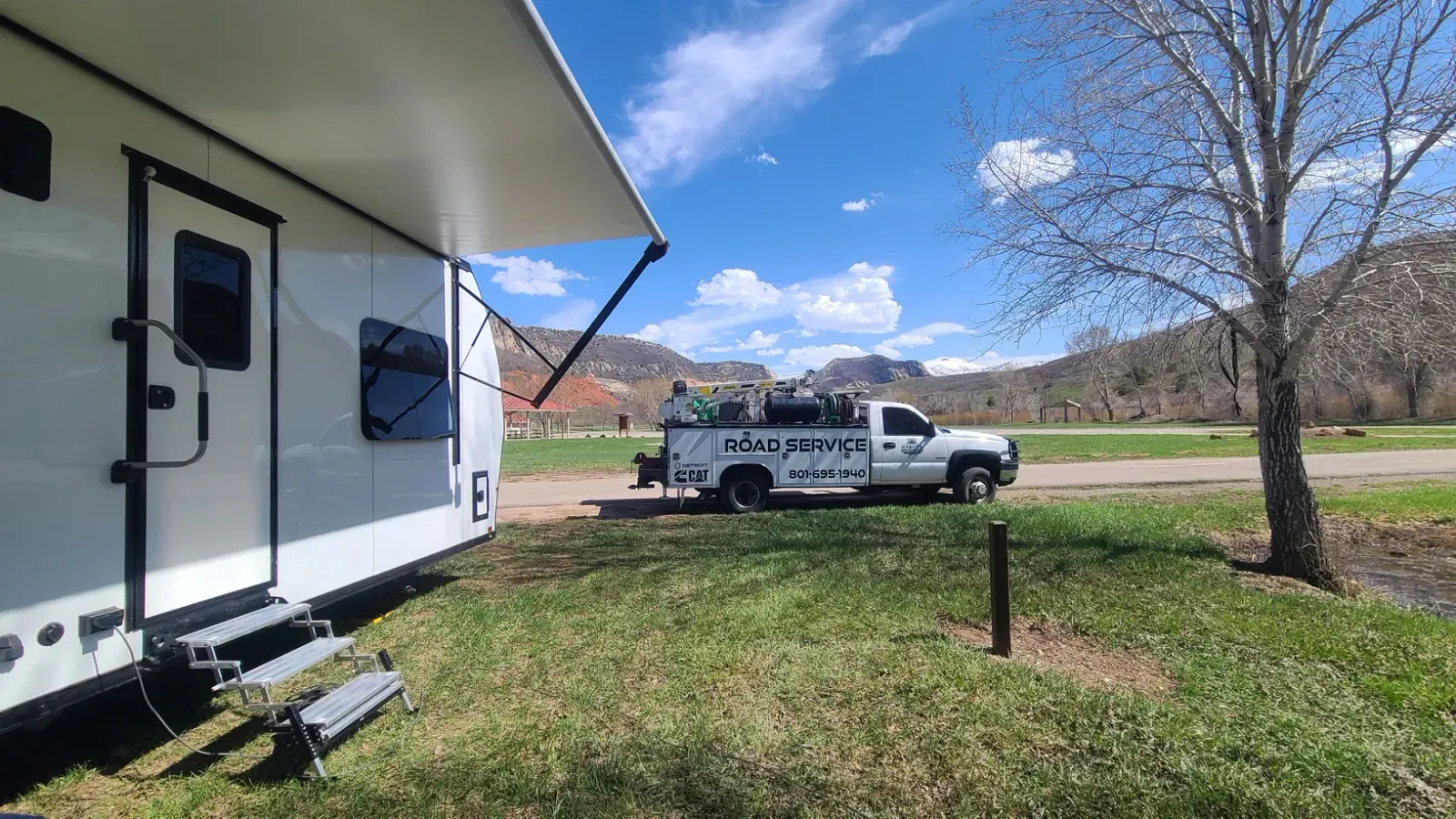
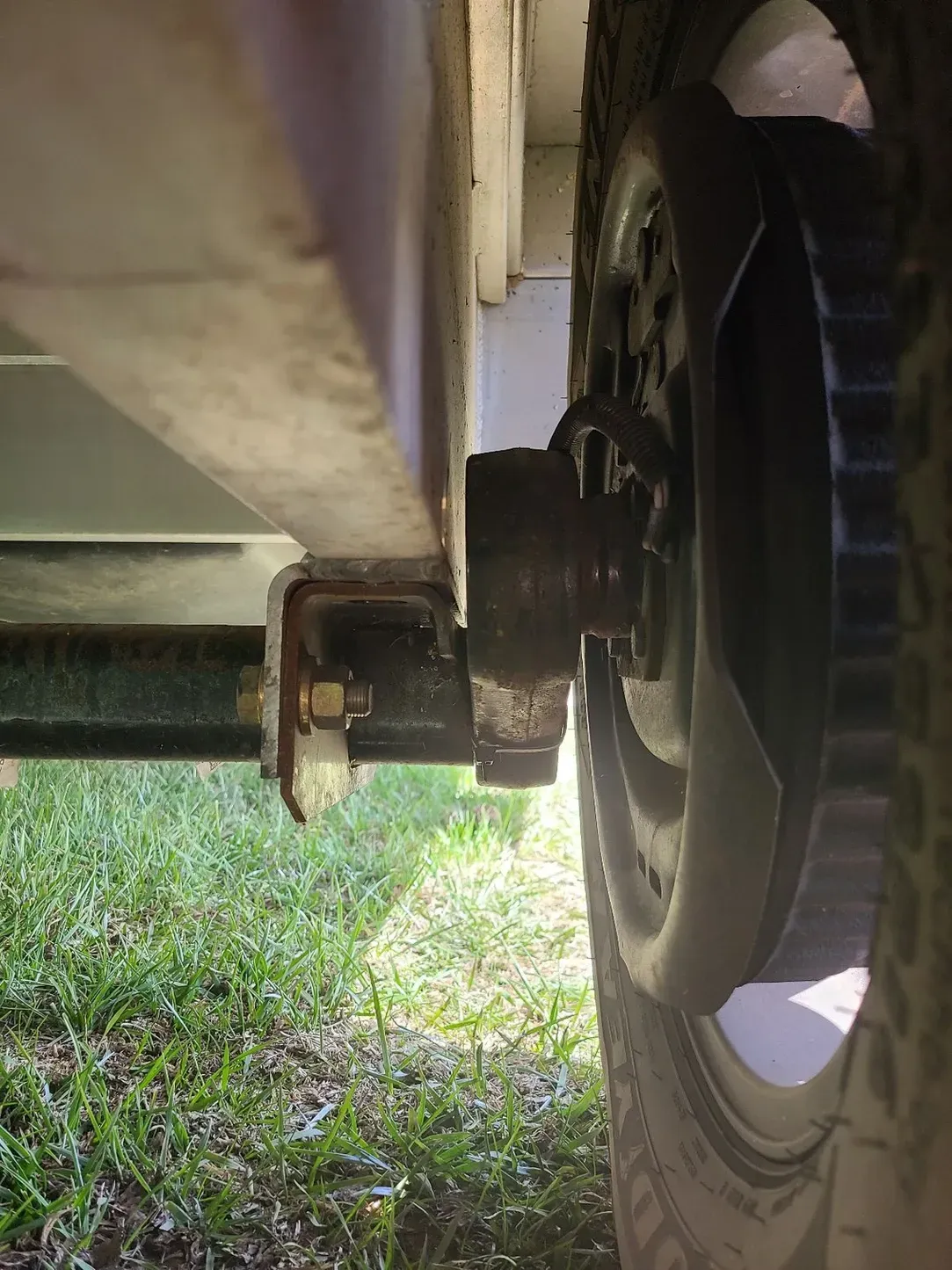
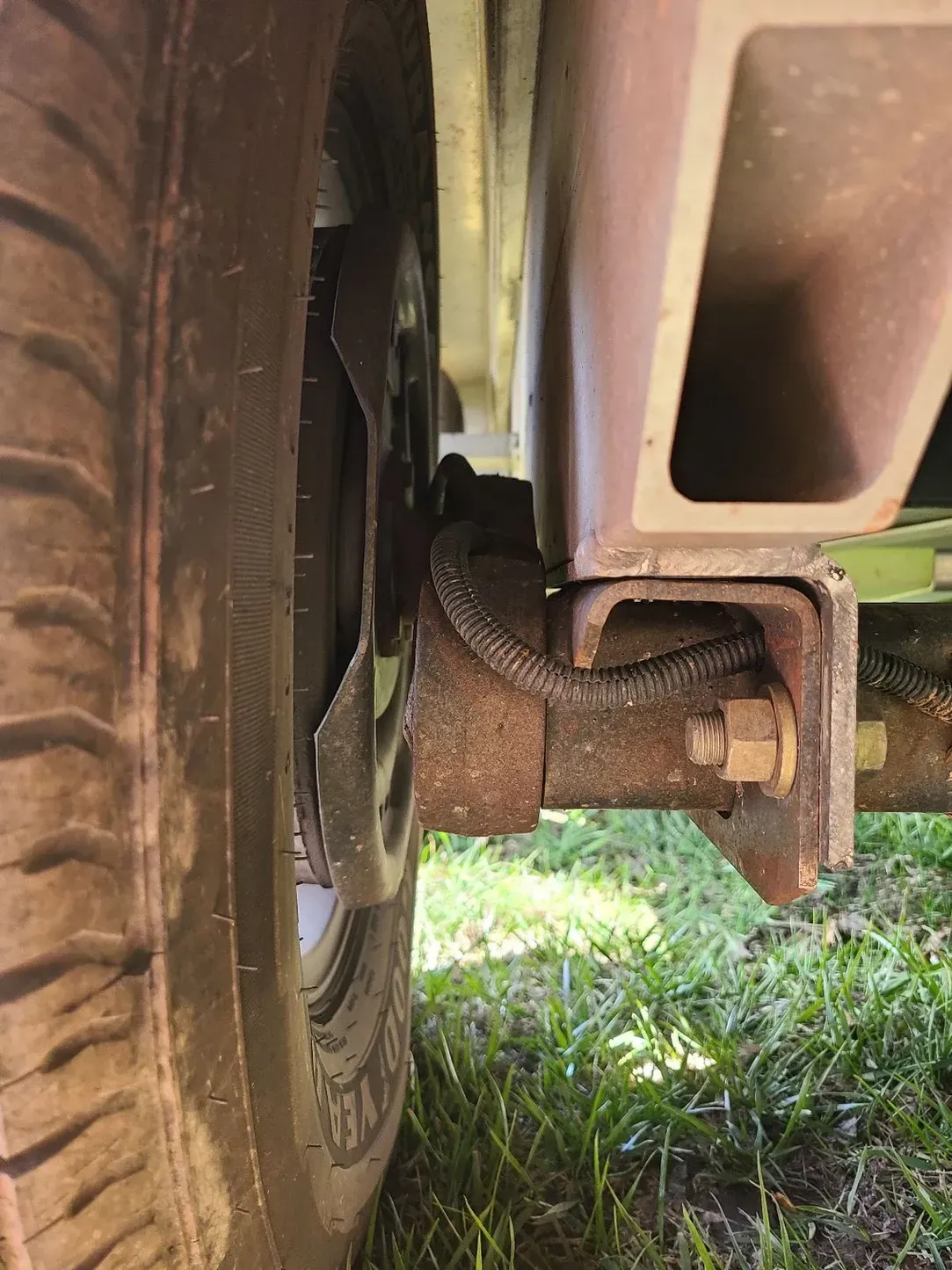
If you've been following our blog, all of this is probably a familiar story. You probably also know that, unlike most RVs, our ATC came with torsion axles. In a nutshell, torsion axles should perform better and give better suspension, but if one part breaks, the whole axle needs replacing. Torsion axles are also not great at keeping the weight distributed if, say, you go over a pothole or dip in the road. The weight can get shifted from front to rear axle, especially if one axle is already bent or busted in some way. This means that when one goes faulty, oftentimes the other has taken the brunt as well, and both need replacing. Still, we're not constantly worrying about broken leaf springs as we barrel down the road, so is it a worthy trade-off?
We had a rather traumatic experience between our assessment and our appointment at FleetPride, but once we recovered our trailer, we moved forward with our axle replacement, counting our lucky stars that they hadn't been replaced yet, or else that would have been a real mess! At FleetPride, we learned that our stock axles, which should have been rated for 6000lb each, were actually rated lower than that. We wondered if this contributed to the problem, but all we could do was add it to the list of possibilities. We ended up upgrading to 7000lb weight rating per axle. When level, we distribute about 5000lb on each axle, so this would give us plenty of room for error.
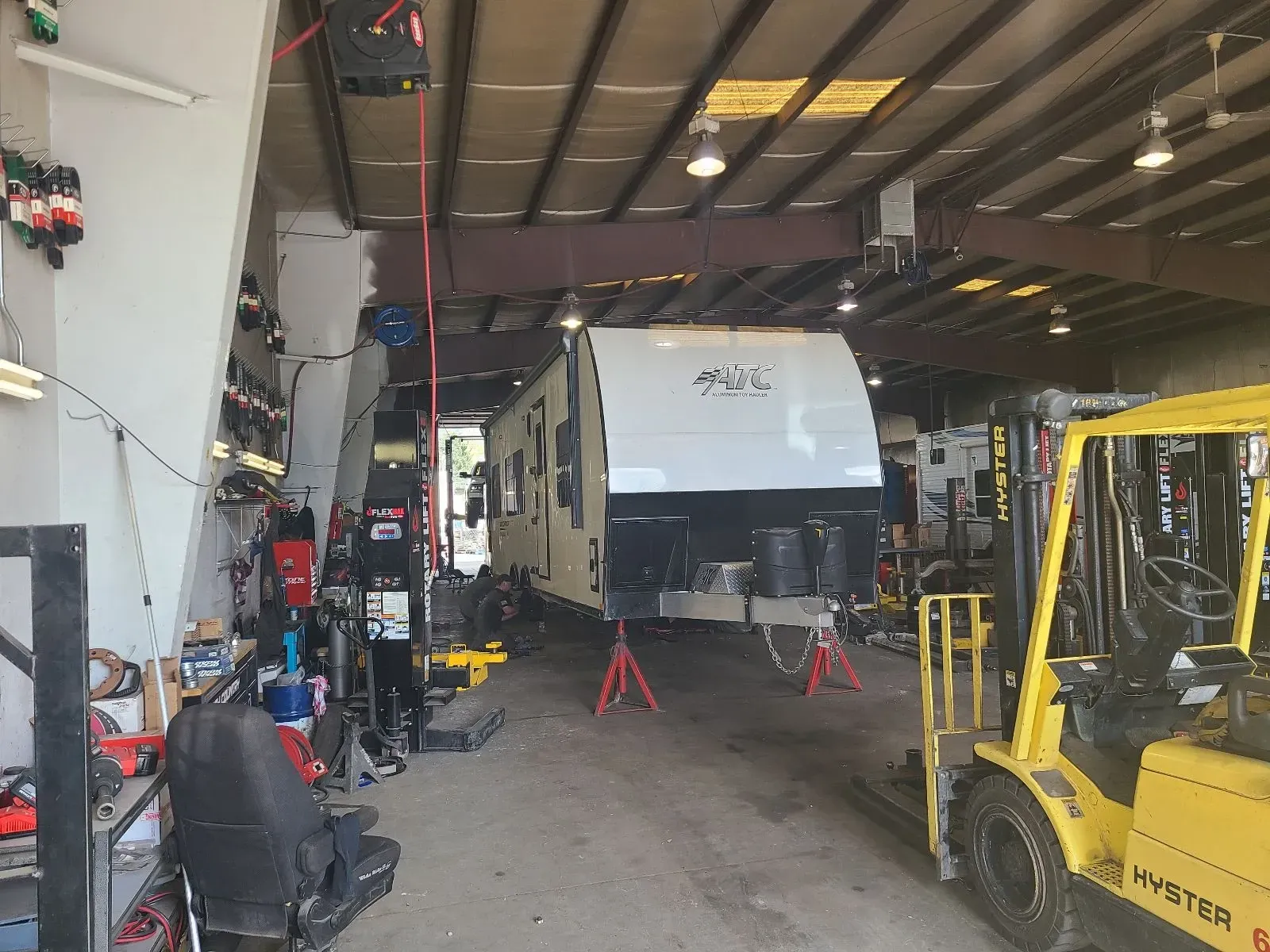
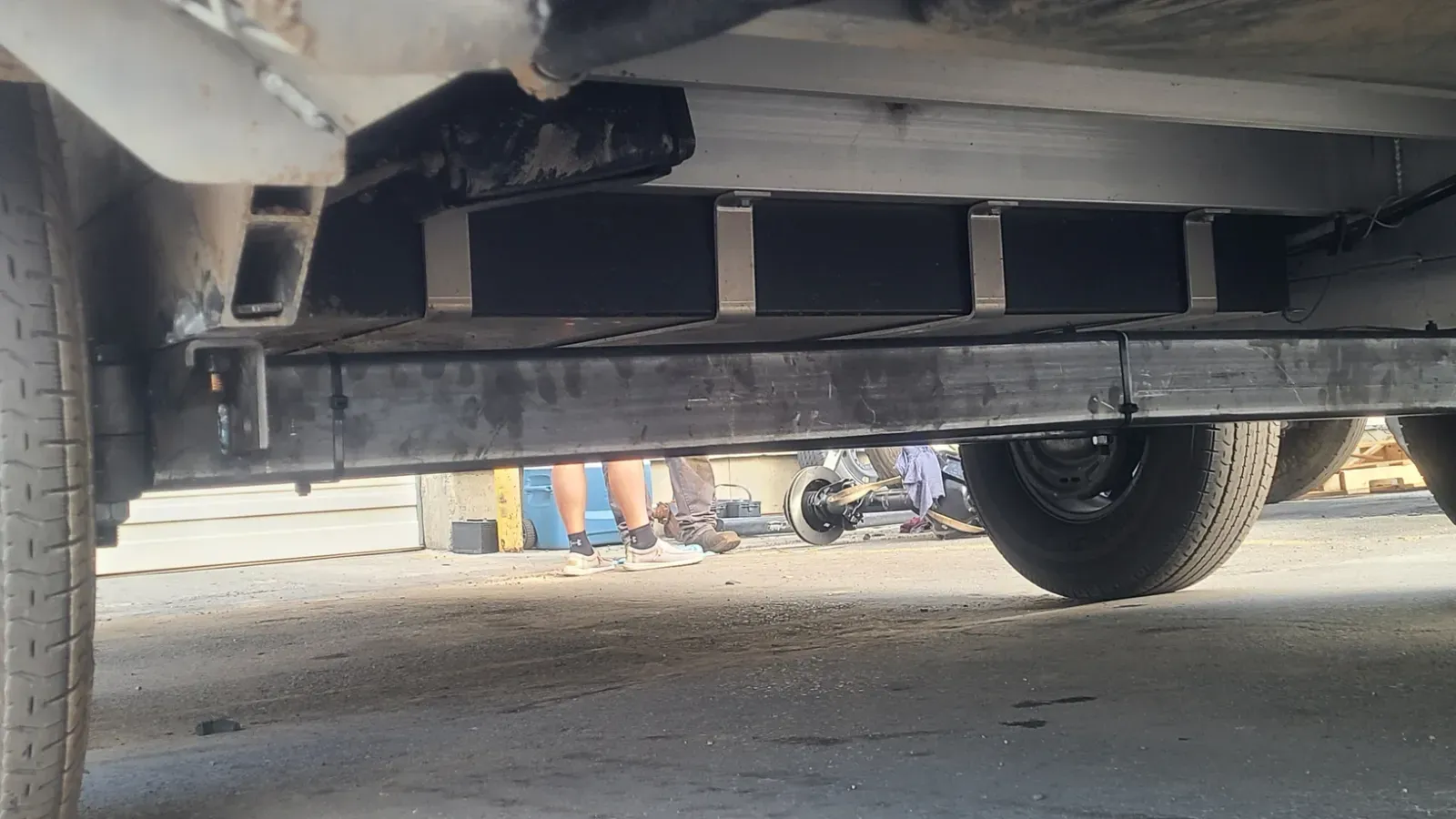
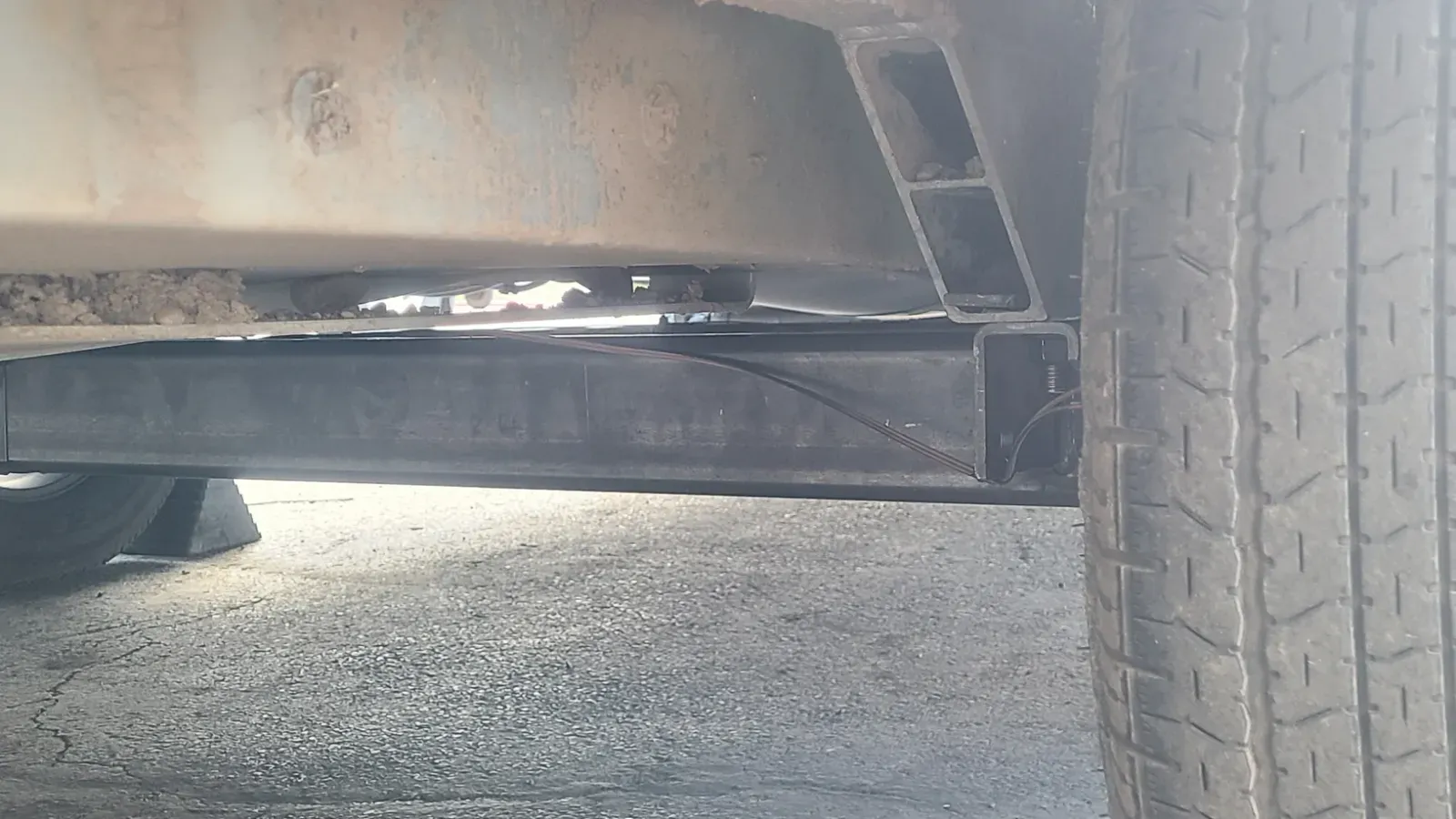
After getting axle set number 2, we made some changes that would affect weight distribution in what we can only assume is a positive way. We got our hitch adjusted properly. We replaced some furniture so that our driver's side has less weight, and we don't store as much under our bed, keeping the front weight a little lighter. All of these changes are miniscule considering the fact that we're not overloaded anywhere in our trailer, we're well under the gross weight rating, and we weren't that uneven to begin with, but we figured there is no harm in being diligent.
We always assumed that this would be the end of the story. We had our new axles, the suspension seemed to be working great, and we had no reason to worry. That was until we set off for Season 3 of travels, and just weeks in, this started happening:
We at first thought that maybe the axles needed cleaning, but cleaning didn't help. We thought that maybe some bearings needed greasing, and so we tucked in the back of our minds that we should probably get to a FleetPride at some point. In the meantime, we continued on with our travels.
Then in April, we began our Harvest Hosts/Boondockers Welcome Challenge, which had us traveling nearly every day, on all kinds of uneven terrain. We also became keenly aware of how much wear-and-tear was happening to our trailer just in this challenge alone. We couldn't push our axles to the back burner any longer. We needed to find a FleetPride.
On the last full day of our challenge, we took the trailer to FleetPride in Fort Wayne, Indiana. Here, we learned that the issue was more complicated than just some bearings needing grease. One axle was tilted and a bunch of components weren't sitting properly. We aren't good with the technical terms, so we'll just say what we said last time: There are gaps where there shouldn't be. See the photos below. The left one is good. The right one is not. The remaining two, not pictured, also had gaps.
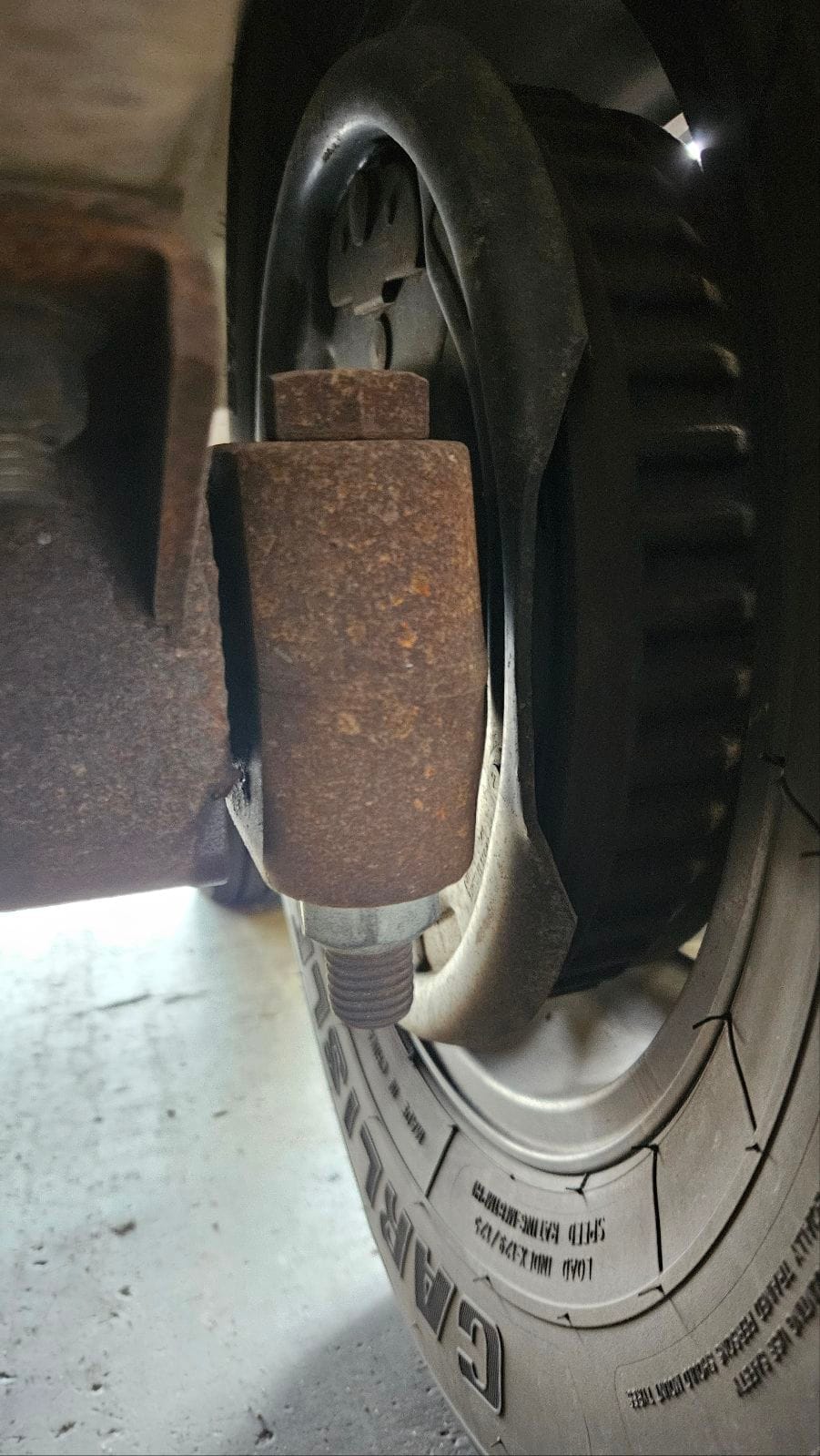
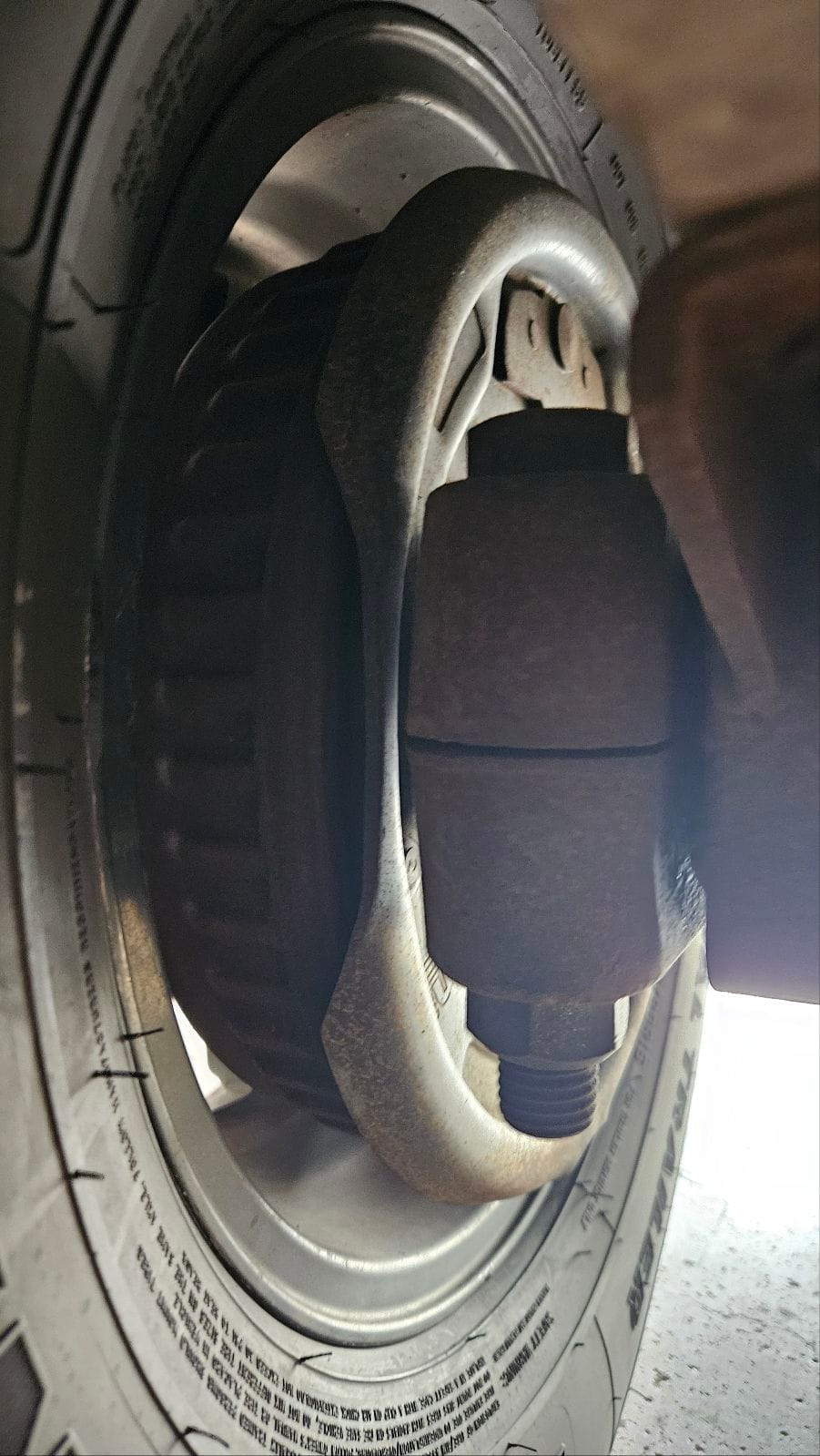
The guys at FleetPride tried to fix the gaps but they wouldn't stay. After getting Utah FleetPride on the phone and discussing the issues, everyone agreed that one of these axles was probably defective, and we might be dealing with the issue of uneven weight distribution where the defective one can't take the weight, so too much gets sent to its counterpart. Really, it was all conjecture, but an educated guess nonetheless. With nothing else they could do, we left FleetPride and creaked our way to our final Harvest Host of the challenge.
We ended the challenge and immediately got ready for a service appointment at ATC that we had booked months before. We had a long list of repairs that seemed to keep getting longer by the day. There wasn't anything we could do about the axles specifically, but the issue was really bothering us. How could we possibly go through two pairs of perfectly good axles in only two and a half years? In our research, we have read everything from torsion axles lasting only 3-5 years, to lasting 15 years or more, no matter how many miles are on them. That's a wide spread, but no matter the numbers, it doesn't help us understand our conundrum.
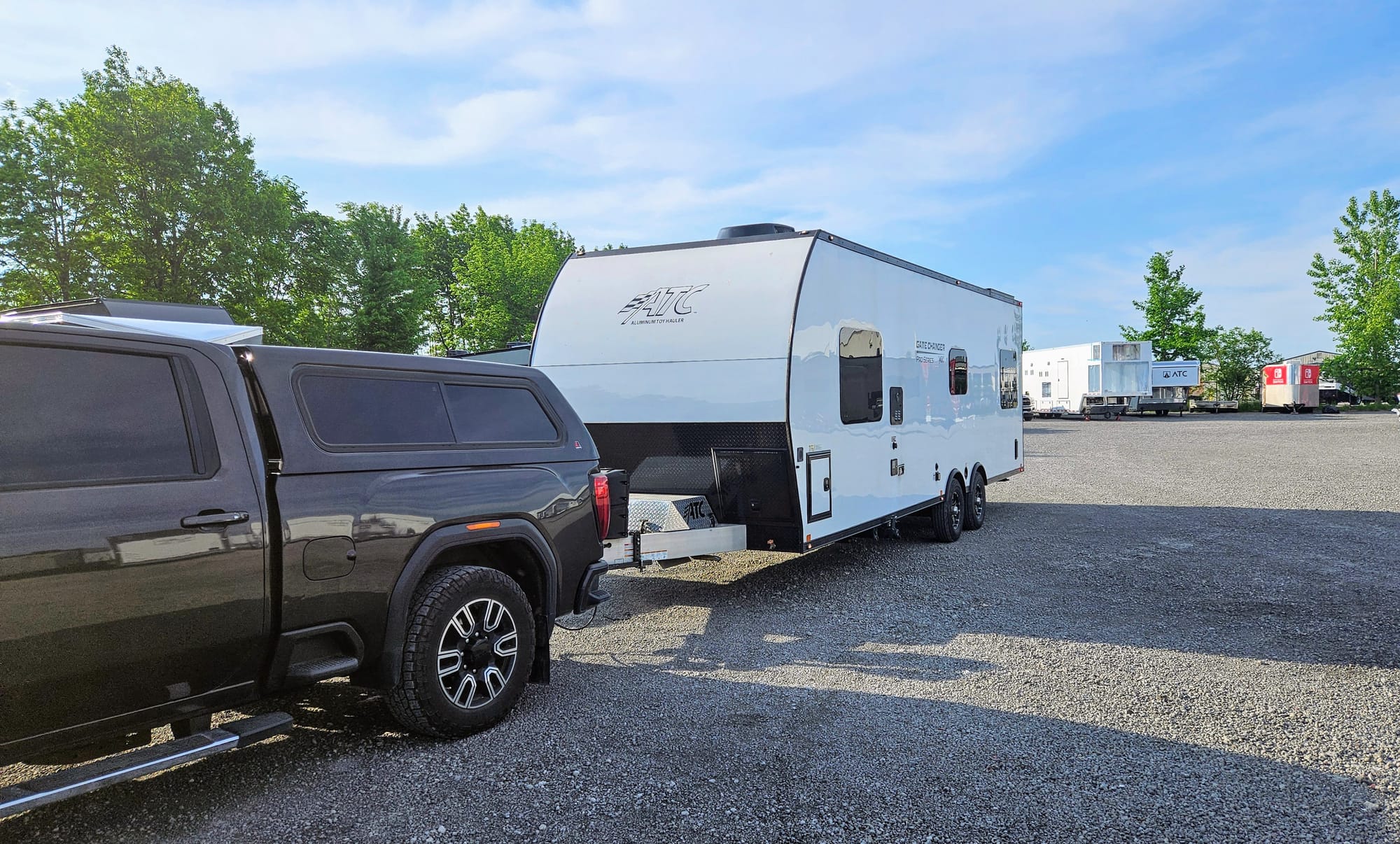
The first time we needed to replace the axles, we had potential reasons to lean on, especially when we found out that they weren't rated as high as we thought. With this next pair, though, we were stumped. The theory that one might be defective really is just a theory; most times even the experts can't tell for sure because it's a component inside the axle. We had a lot of drive days during our challenge to ask ourselves the hard questions. What if our axles keep bending due to a root cause, like a frame issue? If the frame isn't perfectly square, it could be putting excess pressure on the axles when we drive. We couldn't even fathom the awfulness of needing our frame replaced and what that would entail, but we needed to consider the possibility. We asked ATC to check our trailer frame while it was in the shop. The only silver lining was that, if we did need a frame replacement, it would be covered under ATC's 10-year structural warranty. Still, our displacement would be extensive, and we didn't know how we would handle it.
We got our answer when we went to pick up our RV two weeks later. The frame looked fine and we were given the all-clear. This was fantastic news, but it didn't solve the problem of our axles. We would still need these ones replaced, and now it was time to figure out where and when we could get it done. Unlike the first replacement, this time we'd be going through FleetPride's warranty department, and since we got these axles in Utah, everything needed to be done through that location's system. Not ideal, considering we were traveling nowhere near Utah for the foreseeable future. To add to the complications, since the workers were assuming a defect in one of the axles, the axle manufacturer also needed to be involved, because there was a good chance we'd be getting warranty service through them. Our travels were taking us on a loop through the northern Midwest, from Wisconsin, to the Upper Peninsula of Michigan, and then down through the Lower Peninsula. After that, we would be close enough to Fort Wayne that we could continue using that FleetPride for service. We figured it was a safe bet considering they had already helped us and were aware of our problem. Hoping that the axles would be built and delivered to Fort Wayne by our arrival, we made an appointment at FleetPride in mid-July. They told us to expect to be displaced for a couple of days. We held off booking accommodations, but we did cancel our final campsite reservation in the Lower Peninsula in order to give us more time to get down to Indiana. We also booked ourselves an overnight outside of Fort Wayne so we could pack for displacement and make our way to FleetPride early morning the day of our appointment.
Then we waited.
We tried to enjoy Michigan as much as possible, but a lot of our time was taken up talking to FleetPride and figuring out the timeline of everything. There were a lot of hoops to jump through, from communicating with the right people, to figuring out warranty coverage, to the actual build, to the delivery, and then finally, the installation. Time was ticking, and the more days that went by, the more the chances dwindled that the axles would arrive to Fort Wayne on time.
Time eventually ran out. The point came where even if the axles were built that day, there was no way they would get shipped to Fort Wayne on time. We needed to cancel our appointment and face the reality that we'd be driving on these axles for hundreds, if not thousands, more miles. They are not unsafe to drive on, but we know that if one is already tilted, it could get worse. We also know that when we drive, the weight distribution between each axle might not be working properly. We've been monitoring two things on our drive days: Our tires, to make sure they are not showing signs of uneven wear, and the handling of our rig/the movement of our items inside. We want to make sure the suspension seems to be doing what it's supposed to. So far, no uneven wear on our tires. As for the suspension, the trailer seems to be handling well, but the jury is still out on if our "drive day earthquakes" have gotten worse.
We are in for a long road ahead – literally. The plan now is to see if we can get the axles sent to a FleetPride service location closer to home, as we will be spending the last five months of the year in New England. Even though the situation isn't ideal, we've been trying to focus on the positives. We can still travel, and once we arrive to New England, we shouldn't be putting too many more miles on the rig before we get the axles replaced. We will also have more flexibility booking an appointment because we'll be in the area for a longer time.
The other positive was that, now that we didn't need to hang out in Fort Wayne, we had time to kill before our next campsite reservation. We needed to start heading east, but beyond that, we were free to roam wherever our hearts desired. The Ohio Valley was our oyster! Where will we end up? We'll share that in the next blog post.